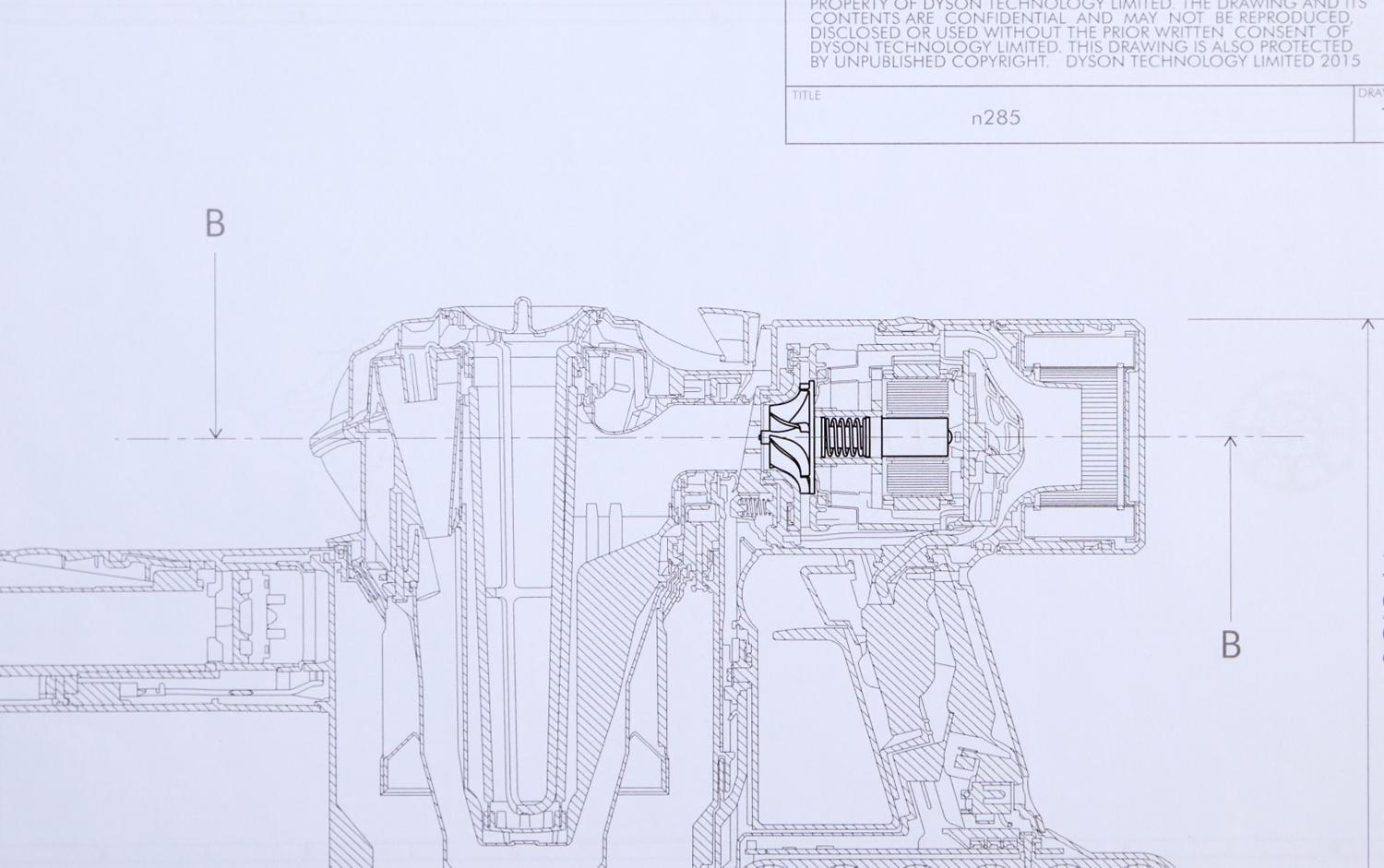
Faire plus avec moins
Par James Dyson
D’instinct, les ingénieurs ont à cœur d’améliorer les choses, de les rendre plus efficaces tout en utilisant moins de ressources. C’est ce que nous appelons « le lean engineering ». Il s’agit de l’une de nos principales philosophies qui nous permet d’utiliser la science et l’ingénierie pour réduire notre impact sur l’environnement. Nous l’appliquons depuis le premier jour, mais nous devons nous perfectionner. Que ce soit par notre technologie de pointe, nos locaux, nos activités philanthropiques, notre travail de recherche ou par la pédagogie auprès de nos collaborateurs, de nos propriétaires et de nos communautés en matière de choix écologiques, il est essentiel que la durabilité soit au centre des préoccupations de Dyson.
Notre mission en faveur du développement durable :
-
1993
La suppression des sacs
Le problème posé par les sacs est simple : ils sont coûteux et polluants, ils doivent souvent être remplacés, ils sont faits de polypropylène, un type de plastique, et finissent à la décharge. Le DC01 a été le premier aspirateur au monde à séparer la poussière de l’air en utilisant la force centrifuge. Il vient à bout de l’inefficacité et des mauvaises performances des appareils traditionnels. Pas de perte d’aspiration, pas de sac, pas de consommables inutiles à usage unique. L’idée a d’abord été rejetée par les concurrents, car les sacs représentaient une source de revenus, mais les consommateurs en ont vu les avantages, et aujourd’hui les sacs appartiennent de plus en plus au passé.
-
1993
L’utilisation de nos cyclones pour capturer les particules
À la fin des années 1980, le Bureau of Mines américain a publié un rapport démontrant que les gaz d’échappement des moteurs diesel pouvaient provoquer des cancers et des crises cardiaques chez les rats et les souris de laboratoire. La technologie des cyclones de Dyson permettait de collecter les particules en suspension dans l’air. Une équipe de chercheurs a donc été mise sur pied pour mettre au point un système de séparation cyclonique pour collecter la suie des gaz d’échappement des moteurs diesel. En 1998, Dyson a dévoilé le dispositif et a contacté les fabricants qui lui ont rétorqué qu’il serait trop fastidieux de se débarrasser de la suie... Mieux vaut donc la respirer ?
-
1995
La fabrication de notre premier produit recyclé
En 1995, Dyson a lancé un aspirateur entièrement fabriqué à partir de plastique recyclé : le Recyclone™. La pratique du recyclage, qui est aujourd’hui très répandue, était toutefois à l’époque inhabituelle et à contre-courant. Le procédé a enthousiasmé les ingénieurs Dyson et nous a beaucoup appris sur les propriétés matérielles du plastique recyclé. Le Recyclone™, d’une durabilité à toute épreuve, n’a malheureusement pas attiré l’attention des consommateurs. Ceux-ci ne le voyaient pas comme un produit "inventif", mais plutôt comme un produit de "seconde main". Comme quoi les temps changent...
-
1998
Le développement des filtres durables
Forts du constat que les filtres jetables n’étaient plus au goût du jour, nous avons entrepris de concevoir des filtres légers, performants et durables. En 1998, nous avons lancé le premier aspirateur Dyson équipé d’un filtre HEPA pour capturer les poussières fines.
-
2000
La conception d’une machine à laver qui consomme moins d’eau
Les machines à laver traditionnelles n’ont qu’un seul tambour, qui tourne dans un sens à la fois, entraînant les vêtements avec lui. Avec si peu d’action de lavage, le linge doit donc tremper dans une solution détergente pour être propre. La Dyson Contrarotator™ a été la première machine à laver dotée de deux tambours tournant en sens inverse, pour reproduire le mouvement du lavage à la main. Résultat ? Des vêtements plus propres plus rapidement, avec une quantité de charge plus importante qui utilise moins d’eau. Le produit a été un succès technique, s’est bien vendu ne s’est pas avéré commercialement viable.
-
2002
La création de la Fondation James Dyson
La Fondation James Dyson soutient l’enseignement de l’ingénierie, la recherche médicale et la communauté locale. À ce jour, elle a fait don de plus de 100 millions de livres sterling (environ 110 millions d’euros) à la cause et plus de 200 000 enfants bénéficient de ses ressources chaque année. Pour inspirer davantage la prochaine génération d’ingénieurs et de designers, nous avons créé le prix James Dyson Award cinq ans plus tard. Depuis lors, il célèbre les jeunes inventeurs du monde entier. 20 % des lauréats ont d’ailleurs réussi à commercialiser leurs idées.
-
2002
La réinvention les moteurs
Les moteurs à haut rendement sont la clé des produits moins gourmands en énergie. En 2002, les ingénieurs Dyson ont commencé à réinventer les moteurs conventionnels. Dyson a ensuite beaucoup investi dans la recherche et le développement pour les rendre plus petits, plus légers et plus efficaces. Le premier moteur numérique Dyson était deux fois plus petit et plus léger que les moteurs conventionnels avec une durée de vie quatre fois plus longue. La vitesse et l’efficacité du moteur numérique Dyson V9 ont permis à Dyson de concevoir son premier produit de soins capillaires : le sèche-cheveux Dyson Supersonic™.
-
2005
Pour des batteries plus propres et plus sûres
Le programme de recherche sur les batteries de Dyson a débuté en 2005. Il se compose maintenant de trois volets de recherche distincts qui couvrent les États-Unis, le Royaume-Uni, le Japon et Singapour. Des progrès en chimie et de nouvelles connaissances en science des matériaux permettent de faire des progrès en matière de densité énergétique, de performance et de sécurité. Les batteries à l’état solide constituent l’un des axes de développement commercialisés : elles offrent un stockage d’énergie plus sûr, plus propre et plus efficace. Sans électrolyte liquide, elles ressemblent davantage à une micropuce qu’à une batterie traditionnelle.
-
2006
La mise sur la touche des essuie-mains en papier à usage unique
Les sèche-mains traditionnels à air chaud n’ont pas changés pendant des années et se sont avérés inefficaces et lents. Quant aux essuie-mains en papier à usage unique, ils représentent une source de gaspillage et ont une grande empreinte carbone sans compter qu’ils ne peuvent pas être recyclés. En expérimentant les « lames d’air », les souffleurs à haute intensité de flux d’air, dotés d’une technologie totalement différente, les ingénieurs Dyson ont constaté l’efficacité du séchage des mains avec les lames d’air à haute vitesse. Les émissions de dioxyde de carbone du nouveau sèche-mains Dyson Airblade 9kJ sont jusqu’à 85 % inférieures[i] à celles des essuie-mains en papier à usage unique et son coût de fonctionnement est réduit de 1/10ème par rapport aux sèche-mains à air chaud traditionnels.
-
2007
La célébration annuelle de l’ingéniosité des jeunes dans le domaine de l’ingénierie et du design
Utiliser la science et l’ingénierie pour résoudre des problèmes du monde réel. Qu’il s’agisse de la mode éphémère, de la restauration ou de l’assainissement de l’eau, le prix James Dyson Award met au défi des jeunes répartis dans 27 pays du monde de mettre au point des inventions qui permettent de résoudre des problèmes. Le prix a soutenu plus de 200 jeunes et le fonds annuel de 30 000 livres sterling (environ 33 000 euros) du prix soutient les lauréats internationaux dans la commercialisation de leurs idées. En 2020, un nouveau prix international du Développement Durable a été créé.
-
2010
L’ouverture de notre première usine de fabrication avancée et hautement efficace à Singapour
La construction d’un moteur quatre fois plus rapide que les autres et effectuant 120 000 trs/min nécessite la précision d’une chaîne de production entièrement automatisée. Les chaînes de production robotisées autonomes de Dyson assurent la qualité et la précision de nos moteurs numériques à grande vitesse, tandis que les processus hautement efficaces réduisent les déchets et augmentent la fiabilité. Il s’agit d’un exemple de machines fabriquant des machines, et aujourd’hui, un moteur numérique Dyson sort de la chaîne de production toutes les 2,3 secondes.
-
2011
Le Centre Dyson pour les soins néonataux a ouvert
Le Centre Dyson pour les soins néonataux du Royal United Hospital s’appuie sur le design et l’architecture pour améliorer l’état de santé des bébés prématurés. La lumière naturelle favorise le rythme circadien et aide les bébés à prendre conscience du jour et de la nuit au fur et à mesure de leur développement. L’unité à faible teneur en carbone est fabriquée à partir de bois lamellé croisé, qui emprisonne le carbone et dont la fabrication est rapide et propre dans un environnement de soins de santé.
-
2012
Les débuts en agriculture
L’agriculture est l’une des formes les plus pures de fabrication. Nous adoptons une approche axée sur le long terme, en utilisant les technologies, les équipements et la recherche les plus récents pour résoudre les problèmes et favoriser l’amélioration. Les fermes Dyson pratiquent une agriculture durable en mettant l’accent sur la santé des sols, la limitation des produits chimiques, le drainage des terres et la biodiversité. Nous produisons de l’électricité à l’aide de nos systèmes de digestion anaérobie et soutenons nos communautés locales.
-
2012
Le plafonnement de la puissance des moteurs des aspirateurs
La majeure partie de l’énergie utilisée par un aspirateur est consommée lorsqu’il est en marche. Dyson a fait campagne pour plafonner la puissance des moteurs afin d’obliger les fabricants à investir dans des technologies à haut rendement énergétique. Au lieu de cela, l’UE a mis en place un étiquetage énergétique trompeur des aspirateurs, qui exagère l’efficacité énergétique des aspirateurs à sac, en les testant vides et sans poussière, bien loin de refléter l’usage quotidien réel. Dyson a contesté cette décision devant la Cour d’appel de l’UE et a finalement obtenu gain de cause.
-
2014
Les débuts d’une production de l’énergie propre à partir de la digestion anaérobie
Nous avons commencé à produire de l’électricité en utilisant la digestion anaérobie au cours de laquelle les turbines sont alimentées par du gaz fabriqué à partir de matières décomposables. Les déchets (appelés digestat) sont utilisés pour fertiliser le sol afin d’améliorer le rendement des cultures. Quant à l’électricité, celle-ci sert à alimenter les foyers et les exploitations agricoles, tandis que la chaleur excédentaire est utilisée pour sécher les céréales. Il s’agit d’un système très efficace.
-
2015
Les premiers pas pour assainir l’air dans les maisons
Le ventilateur purificateur Dyson Pure Cool™, le premier purificateur d’air Dyson, surveille automatiquement la qualité de l’air. En plus de capturer le pollen, les moisissures, les bactéries et les odeurs, il peut piéger les particules ultrafines et projeter un air purifié de manière uniforme dans toute la pièce. Grâce à notre technologie de filtrage améliorée, le purificateur Dyson Pure Hot+Cool Link™ capture désormais les gaz et 99,95 % des particules dont la taille est aussi petite que 0,1 micron, y compris le formaldéhyde, le benzène et les odeurs domestiques.
-
2015
L’exploitation de l’IA pour concevoir des machines intelligentes
L’aspirateur Dyson 360 Eye™ utilise la toute dernière technologie d’apprentissage et d’intelligence artificielle, mise au point par nos équipes de recherche. En utilisant une caméra à 360° pour obtenir une image complète de la pièce, il détermine intelligemment la manière la plus efficace de nettoyer cette zone, afin de ne pas gaspiller d’énergie à passer sur des zones qu’il a déjà couvertes.
-
2016
La restauration de l’aérodrome de Hullavington
Dyson a acheté l’ancien aérodrome de 210 hectares du ministère de la Défense britannique pour développer les activités de RDD au Royaume-Uni. Plutôt que de démolir et de reconstruire, les structures historiques ont été restaurés afin de préserver leur patrimoine historique et de réduire les déchets. L’utilisation du bois lamellé-croisé (CLT) à la place du béton a permis de réduire l’impact environnemental. 8 % de toutes les émissions mondiales de CO2 proviennent de la production de béton, une tonne étant rejetée dans l’atmosphère pour chaque mètre cube de béton. Le bois lamellé-croisé emprisonne le carbone au lieu de l’émettre.
-
2016
L’invention d’une solution plus rapide de sécher les cheveux
Les sèche-cheveux conventionnels peuvent être encombrants, difficiles à manier et souffler de l’air à haute température, ce qui peut causer des dommages dus à la chaleur extrême ainsi qu’aspirer et emprisonner les cheveux dans le filtre. Les ingénieurs Dyson ont entrepris de repenser le sèche-cheveux et ont conçu le sèche-cheveux Dyson Supersonic™. Alimenté par le moteur numérique Dyson V9, il crée un puissant flux d’air pour un séchage rapide. Un contrôle intelligent de la chaleur mesure et régule la température de l’air pour protéger les cheveux des dégâts liés à une chaleur extrême, réduisant ainsi le besoin de consommables supplémentaires pour le traitement thermique.
-
2017
Inauguration par James Dyson du Dyson Institute of Engineering and Technology
Le Dyson Institute of Engineering and Technology propose un autre type de diplôme. Les étudiants Dyson se concentrent sur la théorie des sciences et de l’ingénierie de haut niveau, combinée à l’application dans le monde réel sur des projets réels. Ils travaillent aux côtés d’experts mondiaux dans leur domaine et sortent de l’enseignement supérieur sans avoir à rembourser d’emprunt étudiant, après avoir gagné un salaire tout au long de leur cursus. Bien que rien ne les y engage, l’espoir est qu’ils restent chez Dyson après l’obtention de leur diplôme.
-
2017
La construction d’un véhicule électrique
En s’appuyant sur les efforts précédents pour capter les particules de diesel, les ingénieurs Dyson ont commencé à travailler sur un véhicule électrique à batterie pour aider à résoudre le problème mondial de la pollution automobile, en arrêtant (plutôt qu’en piégeant) les polluants à la source. Ce projet a rassemblé notre expertise en matière de technologie des cyclones, d’aérodynamique, de batteries, de systèmes de vision et de robotique pour concevoir et fabriquer une voiture électrique. Bien que l’équipe ait développé un fantastique véhicule fidèle aux valeurs de Dyson, le projet n’était pas commercialement viable et a pris fin en octobre 2019.
-
2018
La mise au point une qualité de lumière qui dure des décennies
Les LEDs consomment plus de 75 % d’énergie de moins que les ampoules classiques. Cependant, lorsque les LEDs surchauffent, elles peuvent s’estomper et se décolorer. Jake Dyson a résolu ce problème grâce à la technologie de refroidissement Heat Pipe qui permet de refroidir efficacement les LEDs. Un tube de cuivre scellé sous vide évacue la chaleur. À l’intérieur, une goutte d’eau s’évapore, dissipant la chaleur le long du tube lorsqu’elle se condense avant de retourner dans les LEDs par capillarité. Elle assure un cycle de refroidissement sans interruption et sans consommation d’énergie qui préserve la qualité pendant 60 ans.
-
2018
La mise au point une technologie de purification capable de nettoyer toute la pièce en utilisant la moitié de la puissance
Grâce à l’écran LCD qui indique en temps réel l’indice de qualité de l’air, le purificateur d’air Dyson Pure Cool™ détecte et alerte des polluants nocifs dans l’air. 33 % d’air purifié en plus est projeté dans la pièce, en utilisant seulement 50 % de la puissance.
-
2019
La création d’un dispositif de suivi de l’air pour les écoliers
Dyson a conçu des sacs à dos visant à détecter la pollution pour l’étude Breathe London en association avec le King’s College de Londres et l’Autorité du Grand Londres. Ce dispositif portable de détection de l’air permet aux enfants de mesurer la qualité de l’air sur leur trajet entre l’école et la maison.
-
2019
La conception du sèche-mains le plus rapide et ayant la plus grande efficacité énergétique[i]
Notre technologie de moteur et de flux d’air permet au sèche-mains Dyson Airblade 9kJ de consommer jusqu’à 87 % d’énergie en moins que les sèche-mains à air chaud en mode Eco, tout en produisant jusqu’à 85 % d’émissions de CO2ii de moins que les essuie-mains en papier. Sa technologie Curved Blade™, alimentée par le moteur numérique V4 de Dyson, peut déplacer 23 litres d’air par seconde ce qui permet au sèche-mains Dyson Airblade 9kJ de sécher vos mains rapidement, en seulement 10 secondes.
-
2019
La conception d’une technologie pour détruire activement les gaz nocifs dans l’air
Mise au point par les chimistes et les ingénieurs Dyson, la technologie Dyson Cryptomic™ est dotée d’un revêtement catalytique unique, dont la structure est identique à celle du minéral Cryptomelane. Ses milliards de tunnels grands comme des atomes ont la taille et la forme optimales pour piéger et détruire les polluants, tels que le formaldéhyde, un gaz nocif aux propriétés réactives. On le trouve dans les articles ménagers courants, notamment les produits en bois pressé, les produits de nettoyage et les tapis. La technologie Dyson Cryptomic™ décompose ces polluants nocifs, en quantités infimes d’eau et de CO2.
-
2019
L’annonce des plans pour restaurer la centrale électrique de St James dans le nouveau siège de Dyson à Singapour
En tant qu’ancienne centrale au charbon (la première du genre sur l’île) la centrale de St James possède déjà une riche histoire. La prochaine étape sera l’installation de nouveaux laboratoires de recherche à la pointe de la technologie, qui permettront à Dyson d’approfondir ses recherches sur les technologies futures. Tout en doublant les effectifs d’ingénieurs et de scientifiques hautement qualifiés à Singapour au cours des cinq prochaines années, en se concentrant sur l’électronique de puissance, le stockage de l’énergie, les capteurs, les systèmes de vision, les logiciels intégrés, la robotique, l’IA, le machine learning et les dispositifs connectés.
-
2020
La conception d’un respirateur pour lutter contre le COVID-19
Dyson a répondu à la demande d’aide du gouvernement britannique concernant la pénurie de respirateurs au sein du National Health Service (NHS). Concevoir et fabriquer les premiers modèles achevés en seulement 30 jours est un exploit inouï, qui a nécessité la transformation des hangars datant de la Seconde Guerre mondiale de l’aérodrome de Hullavington et la dotation de 450 ingénieurs et scientifiques de Dyson. Il s’agit d’un respirateur à usage intensif, qui permet au patient de respirer en unité de soins intensifs. Il peut aider à l’évacuation des mucosités dans les poumons tout en permettant au patient de respirer.
-
2021
Nous serons neutres en termes de carbone dans les fermes.
L’énergie verte que nous générons dans nos fermes permettent d’alimenter notre flotte de véhicules agricoles, nos fermes mais également 10 000 foyers.
-
Contacts Presse
-
Ennie Bertelli
Email: ennie.bertelli@dyson.com
-